This is part of our Leading through change series. The series explores how manufacturing leaders can succeed in turbulent conditions.
Cost savings can be hard to find. But many manufacturers have potential savings hidden in the production line or parts room.
If you form a map to find these savings, you can improve your tax strategy, operational metrics, bottom line and even top line.
The starting point is a new mindset. Finance and tax strategists often think of “the line” as one big asset under the operations team. Likewise, operations leaders often focus on fixing machines. That’s traditional. But now, we can now do better. We can gather and integrate more data, so that we can better understand the tax and finance impacts of decisions at a more granular level.
That helps us find a path to better financial performance.
The path to better performance is a comprehensive and systematic approach that follows an asset all of the way through its lifecycle. From planning to decommissioning, manufacturers need to:
- capture performance, warranty and tax data about each asset
- gather, update, test, and analyze that data
- embed reminders, triggers, and checklists into assets and processes
The risk of inaction
Some manufacturers have stayed planted in traditional asset management, but that approach has rising risks. “In the Tax Cuts and Jobs Act of 2017, many provisions allowed for essentially 100% expensing of equipment, up until December 31st, 2022,” said Grant Thornton Strategic Federal Tax Principal David Cavin. “In effect, you could recover the cost of that up-front expenditure almost immediately via tax deduction. Those provisions are now starting to step down, so paying attention to the tax treatment of these expenditures becomes increasingly important.”
Similarly, the failure to account for the jurisdiction in which an asset is located can mean forfeiting an exemption on a 7% tax levy. Ideally, a system would flag that exemption and send reminders to file any necessary paperwork. The savings realized can be substantial, especially when compounded over the life of the asset.
There are also operational benefits for a more comprehensive approach to asset management. An integrated, data-rich, end-to-end asset management program could improve overall equipment effectiveness (OEE) by helping you anticipate maintenance needs and optimize replacement schedules based on your real-time data, not general recommendations.
Six steps along the way
Every manufacturer’s path to asset management savings will be different, but there are six primary steps along the way:
- Account for the needs of all stakeholders.
The goal of operations will be to be as predictive as possible — to measure and monitor how you can maximize OEE. The goal of tax and finance will be to optimize tax decisions, to help improve cash flows. An integrated system can do both. - Adopt a lifecycle perspective.
Every asset should be considered at every stage of its life. For example, examine the tax implications of an equipment purchase. “I'm not saying that's the most important thing when you're planning out your acquisition of fixed assets, but it's a best practice and an organization should know what the net cost of that asset would be,” said Grant Thornton Tax Leader Brian Murphy. Grant Thornton Manufacturing Industry National Managing Principal Robert Hersh added, “If you can add that on top of the cash flow analysis, revenue analysis and return analysis, you have something very powerful.”
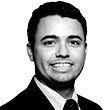
“Devices can be installed on each asset, collecting data that could be monitored and tracked for decisions.”
- Take an integrated view of the asset.
Include operational considerations like maintenance scheduling, replacement timing, downtime prevention and productivity. Tax considerations should include direct and indirect state, local, and national taxes, exemptions and valuations. - Leverage the Internet of Things to move from reactive to predictive maintenance.
“Devices can be installed on each asset, collecting data that could be monitored and tracked for decisions,” said Grant Thornton Transformation Advisory Experienced Manager Alex Mendonca. “For instance, if we can see that the temperature for a molding machine is going up above the standard for that machine, we could potentially predict when the machine is going to go down. You can bring in a team during a planned downtime to fix it and keep the machine up.”
- Strive to be both granular and comprehensive.
Move past looking at the line as one asset, or looking at equipment as simply parts to keep machines running. Start to track any asset with meaningful tax implications given the company’s tax landscape. - Actively interrogate and analyze data.
“Data analysis is critical. Typically, your maintenance department is collecting this data, either going in the file cabinet or, in some cases, into a database,” said Grant Thornton Transformation Advisory Director Ken Deakyne. “But they’re seldom analyzing the data. By having someone analyze the data, from a perspective of tax, asset performance, reliability or skill sets, you can improve asset utilization. That's what asset reliability performance is all about.” That approach can also help refine maintenance schedules, uncover sources of productivity and yield insights into potential changes like line configurations.
These steps can lead to profound benefits. Assets have a significant importance and size for manufacturers, which means there is significant potential for immediate and ongoing gains when manufacturers manage their assets more effectively.
Contacts:
Our manufacturing featured industry insights

No Results Found. Please search again using different keywords and/or filters.