This is part of our “Leading through change” series. The series explores how manufacturing leaders can succeed in turbulent conditions.
Many manufacturers are concerned that ESG initiatives will tie up their resources, increase their costs or lock them into idealistic commitments.
Here’s the good news: You might have done more work than you know — and your next steps to creating value and mitigating risk with ESG might be easier than you think.
Plus, those next steps could be some quick wins, or they could be aligned with your other business objectives. Start by determining what you want to do, and aligning that with your current capabilities.
Identify your goals
To determine what you want to do, review the relevant regulations and discern the expectations of your customers and other stakeholders.
1. What priorities do they have?
2. What metrics do they watch?
Next, appraise your current state. Think in terms of policies, processes, staff, data and metrics.
3. What are you already doing?
4. What are you equipped to do?
5. Maybe more importantly, what are you not equipped to do?
Then, consider factors outside of ESG.
6. What business objectives matter to you?
The business objectives of cost control, resource management, risk management, and compliance often align with ESG objectives. In many cases, they come with best practices and commonly accepted metrics that you might already incorporate into your business. Consider these common ESG topics, along with the associated work and metrics that you might already have:
ESG progress does not have to be a sequential process with isolated steps. In fact, it’s usually more efficient and realistic if steps overlap and inform each other. You’ll naturally spend more time in those areas where ESG priorities line up with your capabilities.
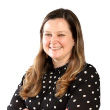
“There's a process of figuring out where the commonalities are, and how you're prioritizing things. As you do that, you’ll start to see a framework that's going to address the most important needs in one piece.”
“There's a process of figuring out where the commonalities are, and how you're prioritizing things,” said Grant Thornton ESG & Sustainability Services Director Jessica Feeley. “As you do that, you’ll start to see a framework that's going to address the most important needs in one piece.”
A theme should emerge:
This is what ESG looks like for our company. This is what aligns with our values. This is what we can do well, and this is what we’re comfortable doing.
Now, you have a theme for an ESG initiative that fits your company. To make progress on your initiative, as with most initiatives, you need to put someone in charge.
Find your leader
There’s not a stock answer about who leads ESG in a manufacturing organization. Your theme will be distinctive to your company, and so will your leadership. Dedicated ESG leaders or teams can be valuable as an ESG program matures, but many manufacturers start by assigning ESG leadership to an existing role.
What’s the essence of your undertaking? Is it a focused risk management or compliance effort? Select a leader from one of those areas. If it’s more social, think about Resource Management or HR. If it touches on several operational units, the COO may be a natural choice. Is it a strategic initiative that depends on data? In those cases, Feeley said, “It's often the CFO. They are connected to measurement and reporting. They have cross-functional access to data and points of contact. They have influence over business strategy.”
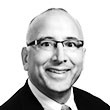
“If the issues are a combination of operations, compliance, or risk, that often sits in the audit committee or even the governance model of a corporation.”
Whoever is chosen should have access to high-level conversations. “Often, manufacturers will dedicate somebody as a temporary or interim ESG leader — but, if they aren’t in the strategic conversations or strategic planning processes, they’re going to be stunted in what they can do,” Feeley said.
Your leader also needs the power to work with the right teams. Grant Thornton Manufacturing Industry National Managing Partner Robert Hersh observed, “If the issues are a combination of operations, compliance, or risk, that often sits in the audit committee or even the governance model of a corporation.”
Make it happen
Most manufacturers will need ESG initiatives to be driven by cross-functional functional teams, often with support from C-suite sponsors. Summarize and finalize what you’re trying to accomplish, which priorities you want to emphasize, and what kind of commitment you want to make. You need to reconfirm that you have full executive buy-in, and be ready to answer some tactical questions:
- What human resources do you need in order to do the initial planning? What are you asking of those resources?
- Is there a sponsor?
- How will you phase in new requirements?
- What policies might be affected?
- What new work will be created going forward and who will do it?
- What metrics matter? What personal and departmental performance metrics might change?
- What qualitative and quantitative data do you need in order to measure metrics? What systems will you set up to track it?
- What technology will you need?
- What’s a reasonable timeline, with milestones for planning, implementation, review and results?
- What’s a reasonable budget?
- What’s the process for reviewing and adjusting your efforts?
- Are there some future factors — like regulations or new plant construction — that you can anticipate now?
It’s easy for manufacturers to be intimidated by ESG. It can feel like you’re being asked to adopt priorities that don’t fit, use resources that you don’t have and make promises you can’t keep.
But it doesn’t have to be that way. Establish a theme that resonates with your values, aligns with your strengths, and dovetails with what you’re already doing. The process may be significantly less painful, and more rewarding, than you think.
Hersh concluded, “We tell clients, ‘There are creative ways that we can make ESG a part of a normal business process. At the same time, you might save energy and improve your cost profile.’” And that’s a priority for every business.
Our manufacturing featured industry insights

No Results Found. Please search again using different keywords and/or filters.